Computational fluid dynamics (CFD)
Engineering
CFD is enabling us to open up completely new possibilities in mesh simulation, impacting on both product development and operational performance. Most importantly, for the first time we are acquiring enhanced process know-how without having to first set up complex and expensive test rigs and metrology.
Using simulations, we can even test the properties of steel meshes and sintered laminates which do not physically exist yet. Simulations can often demonstrate whether it is worth continuing with the development, which plays an important role in reducing development lead times, cutting down on test procedures and saving on development costs. Alongside the introduction of new developments, simulations deliver important information on operational performance and thereby on optimisation potential for our meshes and filter elements installed in machinery, individual assemblies and single components.
Using CFD means that aspects can be tested which under certain circumstances are not definable even with advanced measuring equipment, including the mapping of actual flow conditions of fluid, throughput and geometry. In addition, individual and specific physical marginal conditions or effects can be examined in isolation. Both of these approaches lead to enhanced understanding of processes and thereby to secure and efficient product development and process control.
The most important advantage, however, lies in the economic efficiency of CFD. Not only can preliminary design of meshes and filter elements proceed to the first stage without the need to build prototypes, CFD also saves many long and complex series of tests on equally complex and expensive test rigs.
Equally, CFD enables fast parameter studies and achieves the same results as many weeks of trials on test apparatus.
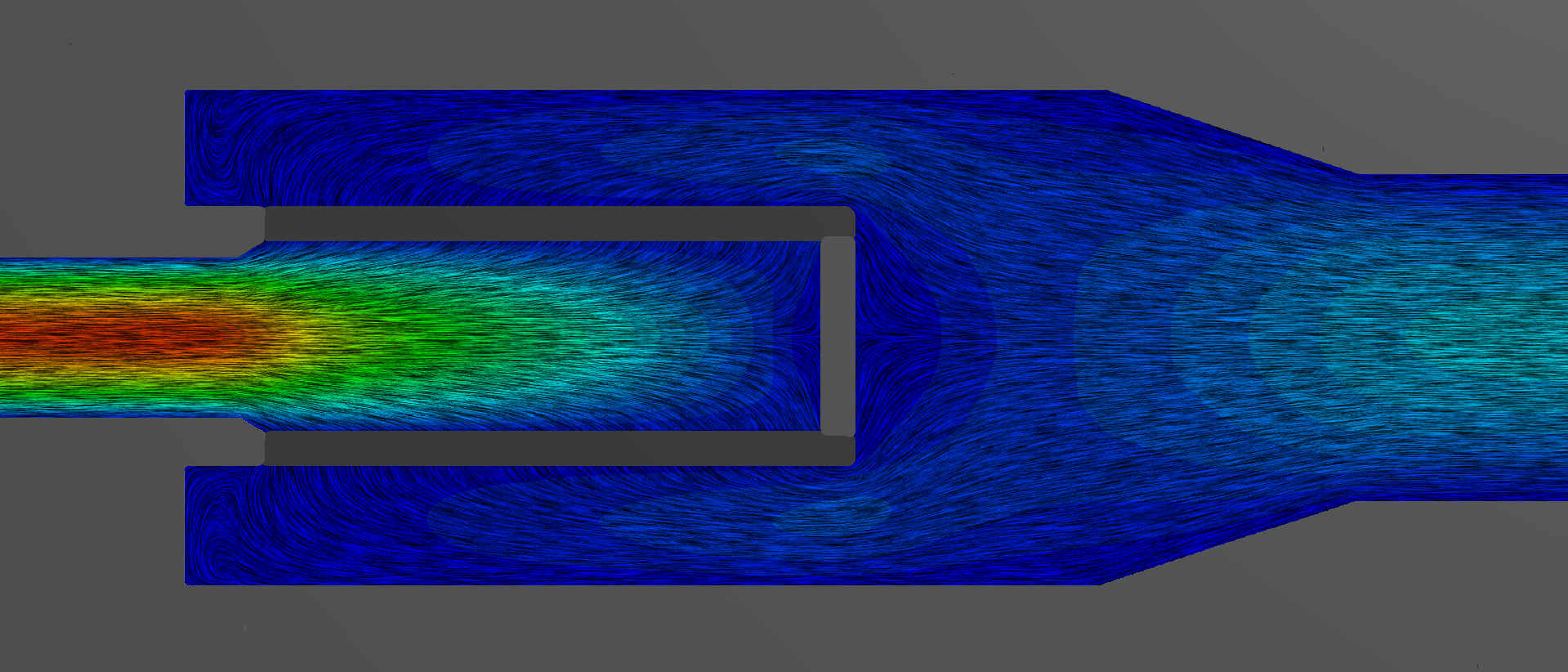
Significant benefits of using CFD:
- Virtual mesh design on a micro scale
- Virtual filter element design on a macro scale
- Calculation of geometric pore sizes
- Analysis and optimisation of flow characteristics for wire mesh / mesh laminates / entire filter elements for customer specific applications
- Analysis and optimisation of separation behaviour for wire mesh / mesh laminates / entire filter elements for customer specific applications
- Geometric optimisation of entire filter elements to reduce pressure drop and therefore improve energy efficiency in the filtration process
- Optimisation of flow control and elimination of dead zones
Here for you.
How can we help you?