Know-How
SCREEN PRINTING TECHNOLOGY
Our recommendations are the result of many years of collaboration with customers, suppliers and partners from the entire screen printing process. With the ever-increasing requirements, for example in electronics, the factors in the entire process are constantly being further developed and optimised. Our specialists will be happy to advise you on special requirements.
Choosing the right screen printing frame
Metal frames must always be used with BOPP SD stainless steel meshes.
- Stainless steel meshes are always tensioned to higher values than synthetic meshes.
- The screen printing frame must be able to take up these higher tensions and maintain these levels over many printing cycles.
- We recommend the use of cast or hollow aluminium profiles.
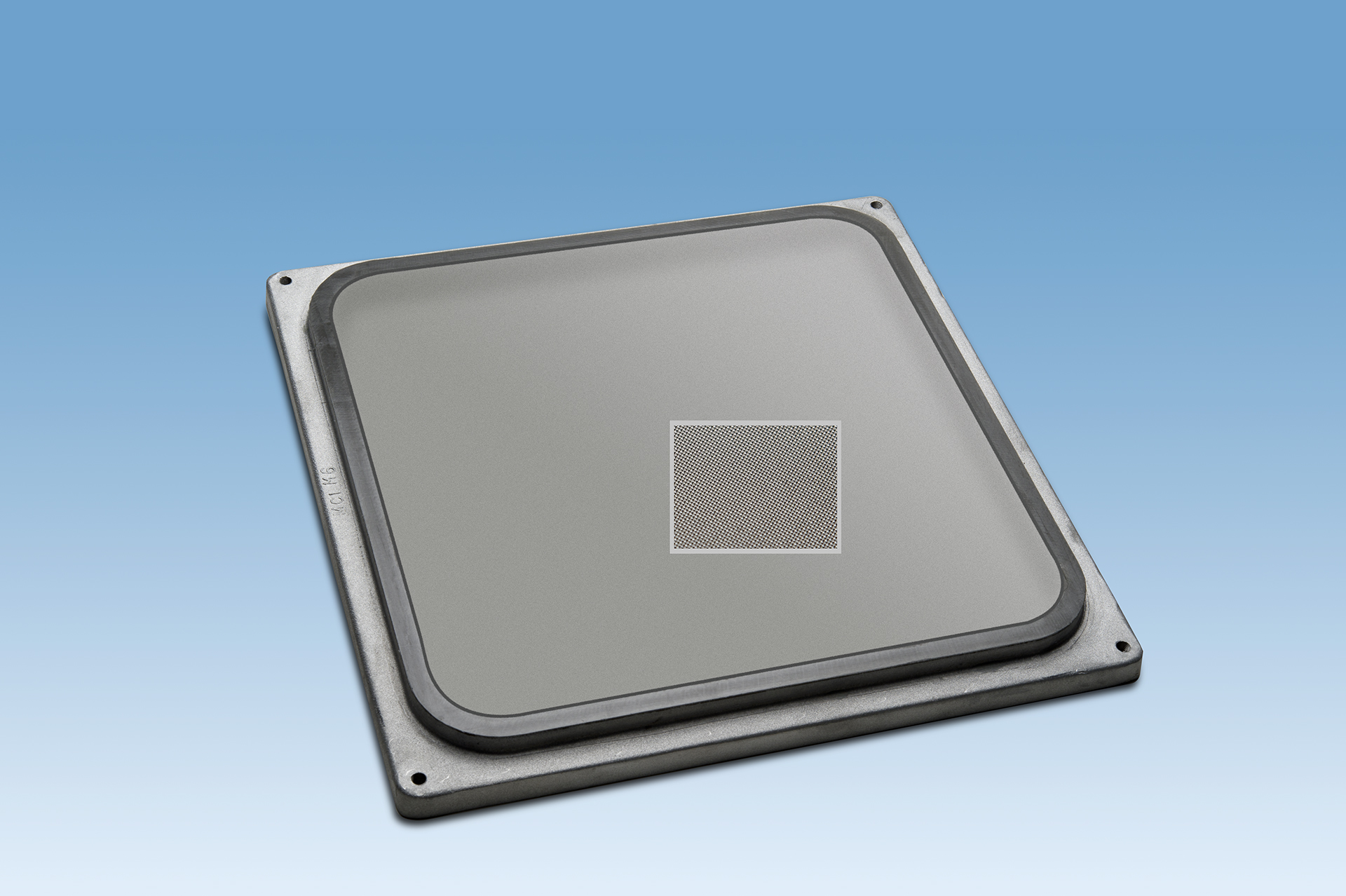
Frame size - a vital factor for durability
- Frames that are too small lead to excessive stress on the mesh
- Fatigue leads to reduced print quality
- Shorter service life means higher costs
Correct tensioning extends service life
- In order to optimise the benefits of today’s modern meshes, a correspondingly productive tensioning machine is required.
- When tensioning, the following rules have proved useful:
1. Bring the mesh up to the required tension in stages. Alternate tensioning in warp and weft directions, always beginning with the warp.
2. During the tensioning process, monitor the tension values using a reliable tension meter.
3. Leave to stand for 15–30 minutes, test again and tension accordingly.
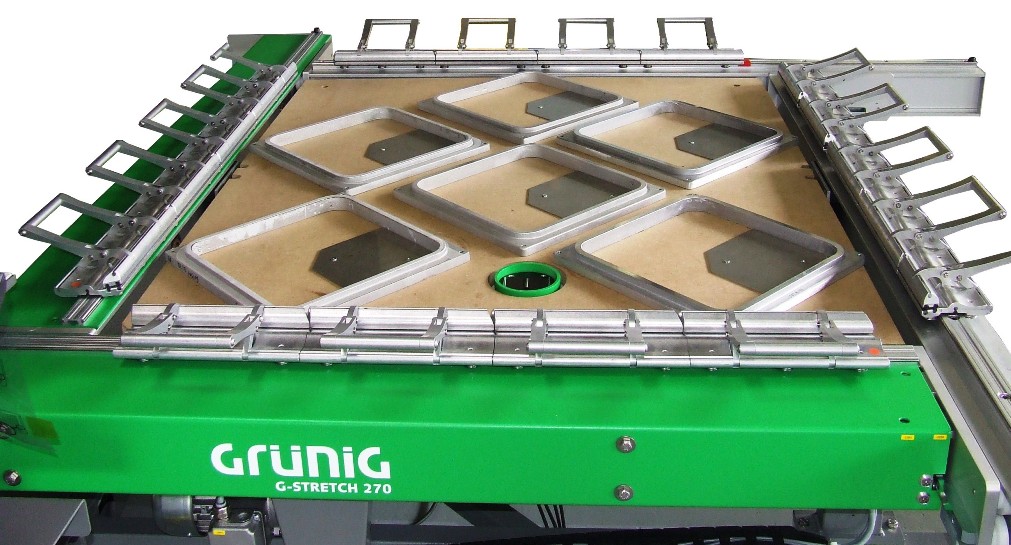
Aligning the mesh
From a mechanical point of view, tensioning at a 45° angle is recommended for reasons of stability. For typographical reasons, this angle is not always ideal. We recommend:
- Where possible, tension meshes diagonally (22° to 45°).
- If diagonal tensioning is not possible, align the weft direction of the mesh with the squeegee.
Producing the stencil
Recommended tensioning for BOPP SD stainless steel meshes is dependent upon the demands upon print quality. Certain BOPP SD and BOPP SD PLUS meshes can be tensioned to way above 35 N/cm. In these instances, the stability of the screen printing frames in use must always be verified. Generally speaking, for these specifications a tension value of 30-35 N/cm is sufficient for an acceptable end result.
- Due to their higher tensile yield point, stainless steel meshes can be tensioned to higher values.
- Higher tensions enable a smaller off contact distance.
- The smaller the off contact distance, the better the registration accuracy.
With careful degreasing, the surface of stainless steel meshes offers an exceptional bond for a wide range of films and emulsions; no napping is required.
SD stainless steel meshes offer minimal undercutting and can therefore be exposed without problems.
Printing (Off contact distance and squeege pressure)
The required off contact distance is dependent upon many different factors such as mesh tension, colour viscosity, squeegee speed and even the print image itself. For this reason, we cannot give general recommendations for off contact distance and squeegee pressure. However, the following is worth noting:
- Always begin with the smallest possible off contact distance.
- If the ink is not released cleanly from the stencil, increase the off contact distance in small stages.
- Always work with the minimum squeegee pressure.
Printing with off contact distance
When printing with off contact distance the mesh will deform, which impacts negatively on registration accuracy. The smaller the off contact distance, the less the deformation and therefore the better the registration accuracy.
- The higher the mesh tension, the lower the ink viscosity and the slower the squeegee speed, therefore a smaller off contact distance is better.
- Doubling the off contact distance results in a fourfold distortion of the image.
Here for you.
How can we help you?